Why Rotomolding is Ideal for Creating Complex Plastic Shapes
Why Rotomolding is Ideal for Creating Complex Plastic Shapes
Blog Article
Rotational molding, or Rotomolding, has turned into a chosen production approach for producing sturdy and supreme quality plastic parts. Its unique process, which requires heat and spinning components inside a mold, guarantees consistently distributed strength and uniformity in the ultimate product. That blog considers the incredible advantages of Rotational Molding and why it has received prominence as a technique for making difficult and long-lasting plastic components.
Remarkable Energy with Uniform Wall Depth
One of many critical skills of rotomolding is based on their ability to produce areas with uniform wall thickness. Unlike other production methods that will leave bumpy or slim areas susceptible to weakness, rotomolding guarantees uniformity atlanta divorce attorneys layer. By consistently heat and turning the form, the molten resin moves efficiently, creating easy and effective plastic pieces that may tolerate large masses and resist impact.

This feature makes rotomolded pieces ideal for applications requesting structural reliability, such as for example big tanks, playground gear, and industrial containers.
Enhanced Durability with Stress-Free Molding
Strain can destroy plastic pieces, impacting their lifetime and performance. Fortunately, the rotomolding process removes central worries often present in other molding techniques. Since number high-pressure causes are employed throughout manufacturing, the plastic material experiences small strain, producing a stronger product that works easily around time.
Moreover, the lack of stitches or weld lines increases the general toughness of rotomolded parts, creating them immune to breaking, splitting, and environmental use and tear.
Excellent Freedom and Customization
Rotomolding offers unparalleled design flexibility, allowing makers to produce complex shapes and structures with precision. The capability to integrate added characteristics like bones, positions, or consistency ensures that the last solution matches particular practical or visual requirements.
This technique also helps the usage of a wide variety of resources and additives, such as for example UV stabilizers and colorants, more boosting durability by making components resilient to facets like sunshine exposure, falling, and compound damage.
Resilience in Serious Conditions
Rotomolded pieces are developed to last, even when confronted with extreme environments. They keep their strength in hard temperatures, resist rust from substances, and endure extended outdoor use. This makes them specially useful in industries like agriculture, structure, and maritime applications, where parts experience complicated conditions daily.
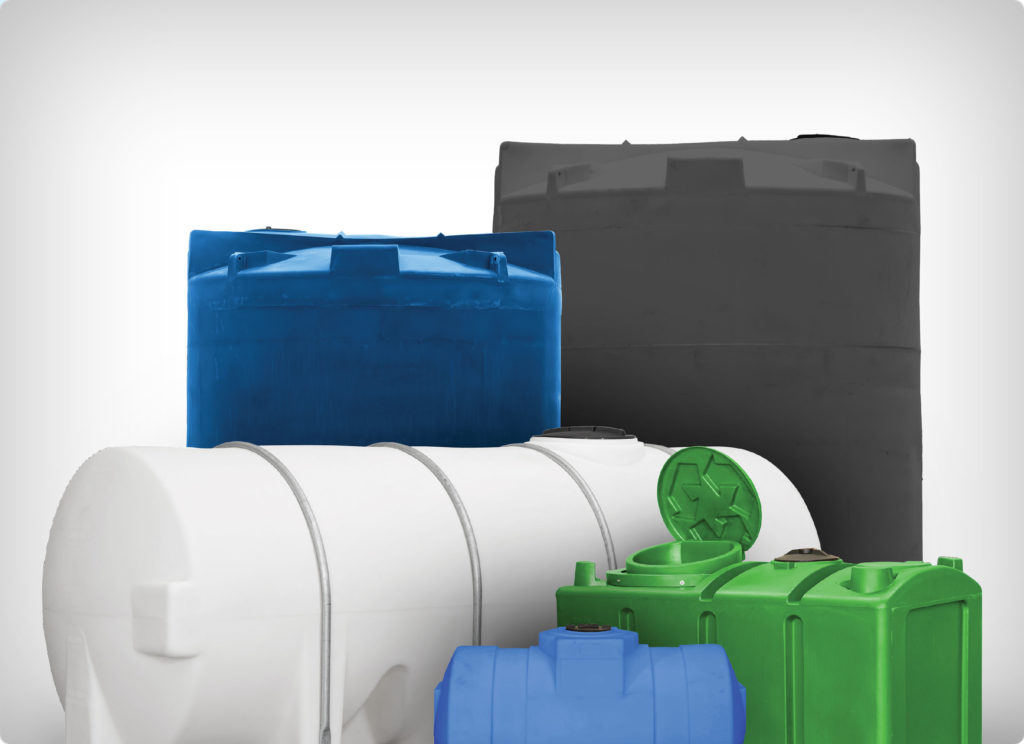
Their capacity to execute dependably such settings decreases the necessity for regular alternatives, creating rotomolded parts both cost-effective and sustainable.
Driving the Potential of Resilient Pockets
The raising need for trusted and durable plastic parts continues to put rotomolding at the lead of manufacturing innovation. With its precision, stress-reducing benefits, and power to resist varied settings, rotomolding is shaping the way industries prioritize power and endurance in their products. By buying this advanced process, makers can make plastic elements that stand the test of time.
Report this page